schattigedieren.nl
VIMM streeft er naar een no-nosense partner te zijn die zich helemaal vastbijt in het mogelijk maken van uw visie.
Geboren uit passie voor techniek, uitdaging en een onverzadigbare nieuwsgierigheid.
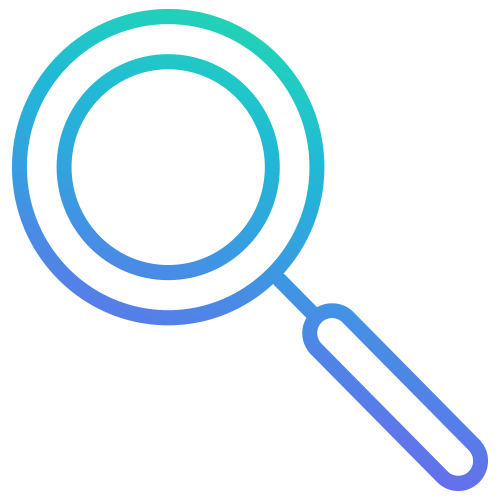
Website in opbouw
De website "schattigedieren.nl" is momenteel nog in opbouw.
Bekijk ook
- bopets.eu - Bopets dierenwinkel met meer dan 12.000 producten online. Alles waar je huisdier gek op is!
- dierencomfort.nl - Dierencomfort de online dierenwinkel voor Nederland.
- dierennamen.net - De mooiste namen voor alle huisdieren.
- diezoo.com - Diezoo gaat dagelijks voor jou op zoek naar de goedkoopste prijs in dierenartikelen.
- kattenclub.be - Online webmagazine voor katten-liefhebbers.
- mooiespreuken.net - Spreuken en gezegden voor elke dag!
- mysticwonderland.be - Website voor een Shih-tzu hondenkennel.
- nieuwehond.nl - Het grootste Online hondenmagazine voor België en Nederland waar honden en hondenliefhebber centraal staan.
- nieuwekat.nl - Het grootste Online kattenmagazine voor België en Nederland waar katten en kattenliefhebbers centraal staan.
- paard.net - Alles over paardensport, vrijetijd, mensport, dressuur, springen, trec, voltige, endurance en nog zo veel meer...
- tuin-info.nl - Alles over tuinen en groene vingers vindt je op Tuin-inf.nl
- tuinkruiden.net - Een andere dimensie met kruiden leer spiritueel omgaan met de kracht van kruiden.
Contacteer ons
Een vraag of een voorstel? Contacteer ons vrijblijvend!